We love what we do.
It’s our passion.
Our innovative company is redefining the art of banjo making, drawing inspiration from the golden era of the 1920s in the USA while infusing it with a touch of Irish magic. Founder partner John McClenaghan has a passion for preserving the rich legacy of the tenor banjo, now and into the future years. His dedication, precision and unparalleled craftsmanship are reminiscent of the banjo makers from the 1920’s. Each of our banjo are a labour of love, meticulously crafted to produce unparalleled resonance and tone.
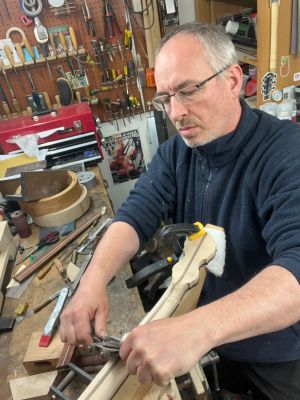
John McClenaghan
I’m John, a banjo builder based in Motherwell, Scotland and I’ve been repairing and latterly, hand-crafting my own instruments for the last 20 or so years. My interest in banjo making follows a path familiar to many Trad Irish banjo players, having been influenced at a young age by the few banjo recordings available back in the day, including the likes of Barney McKenna of the Dubliners and Liam Farrell in London. A decent banjo in those long gone, pre-internet days was often difficult to obtain, far less maintain or repair, and so, my banjo building journey started initially by doing my own adjustments and repairs, moving on to banjos which I constructed from imported parts and finally designing and hand-crafting my own instruments.
My interest in banjos now spans all genres of music, from Trad Irish to Dixie Jazz and Bluegrass, but the one constant is my use of superior and sustainably sourced tonewoods and materials to produce a quality traditional banjo which embodies the very best attributes found in the classic banjos of the pre-war era. I constantly strive to achieve a well-balanced sound with depth of tone, clarity and levels of sustain which permit the player to express and enhance their own style and innovation, whatever that may be. I pay particular attention to the neck profile as well as the overall weight distribution of the banjo which offers the player comfort and playability, putting them in complete command of the instrument.
Whilst I am in the process of designing various grades of banjo, I’m always happy to listen to and work with customers to achieve the instrument they desire. Every timber component of my instruments, as well as the decorative inlays are hand-crafted by me alone at my workshop. I do not use CNC machines, and make only minimal use of general woodworking machinery. For this reason, I only have the capacity to make a limited number of instruments per year, however, I believe that this allows me to produce banjos of individual character, reliability and ultimately, a lifetime of enjoyment for the player.

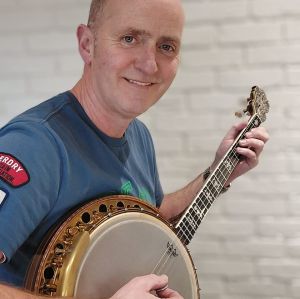
Paul Conlon
I’m Paul, a banjo restorer or as some say ‘Banjo Mechanic’ based in the North of Ireland. I’m very passionate about restoring vintage banjos especially from the 1920’s jazz era. I also provide a banjo setup service at my home workshop and have many regular professional & amateur banjo players that avail of my service.
I’ve taught banjo at the Andersonstown School of Music, Belfast Trad and currently teach at GSOTM. I know how a banjo should sound and each and every one of them have their own characteristics. So getting the right tone, volume and sustain takes many hours with some setups. I’ve always aimed to begin building my own banjos and I believe the time is right to do so. I teamed up with John over a year ago and we both put our heads together and come up with 4 new banjo designs. These new banjos will be totally built with the UK which we are proud of. Check out our ‘News Page’ for the latest updates.
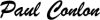
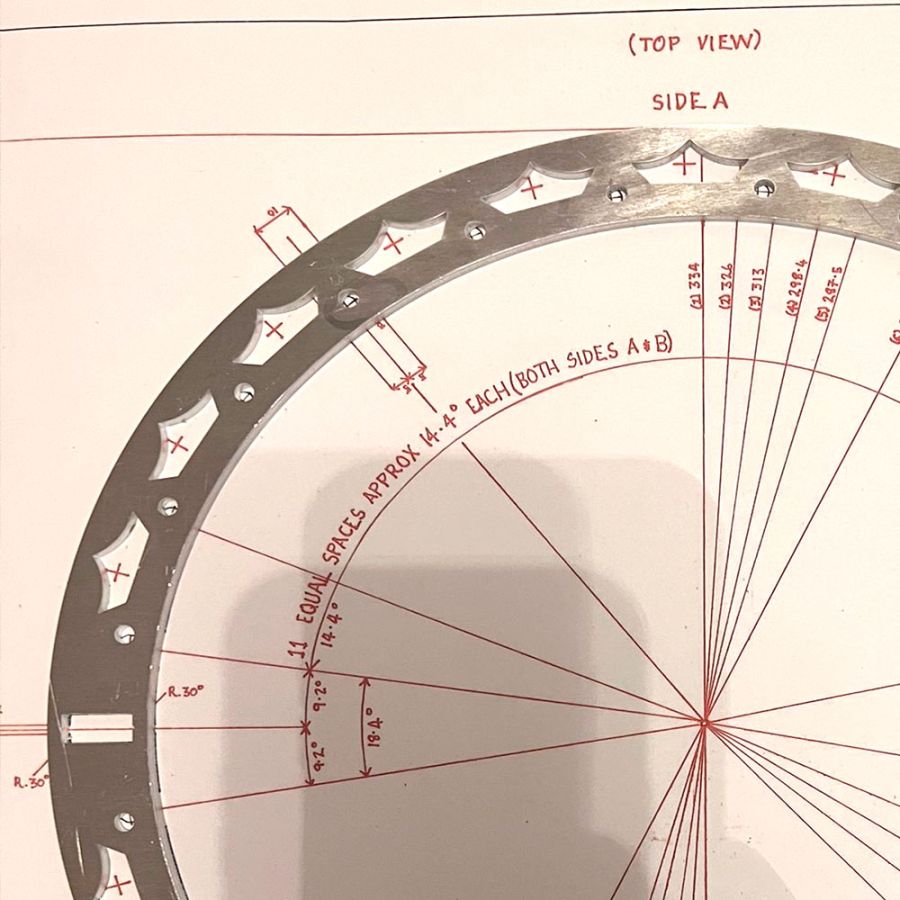
Starting with an idea and transforming it into detailed drawings
From a simple doodle on paper to transforming it into detailed drawings is a pivotal process in the creation of our banjo parts. The accuracy of the initial drawings are crucial before taking them to the CAD stage to create DFX. files. We use local engineering companies based in Lisburn to produce both water jet and laser cut flanges.
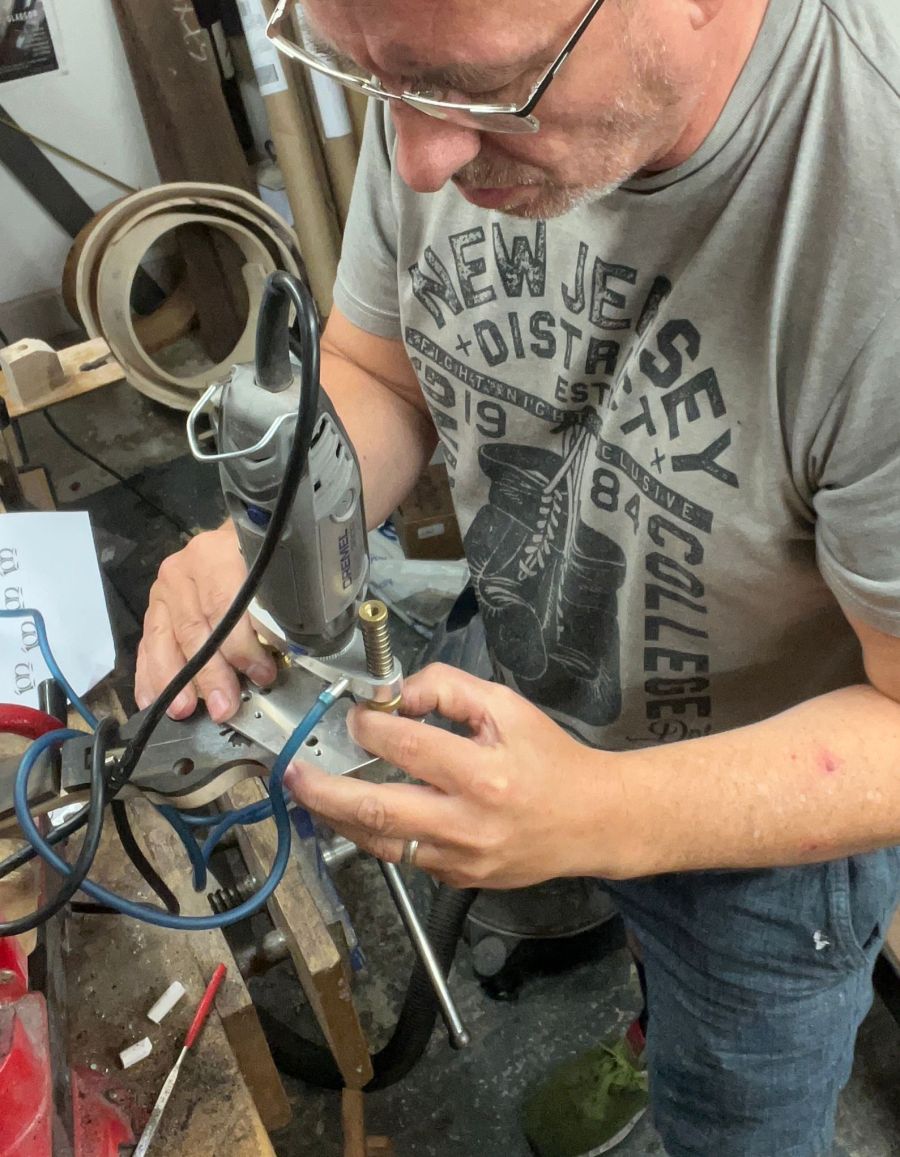
Hand cut pearl inlay
Hand-cutting pearl inlay for headstocks and fretboard involves a combination of skills that require precision, attention to detail, a blend of artistic flair and craftsmanship.
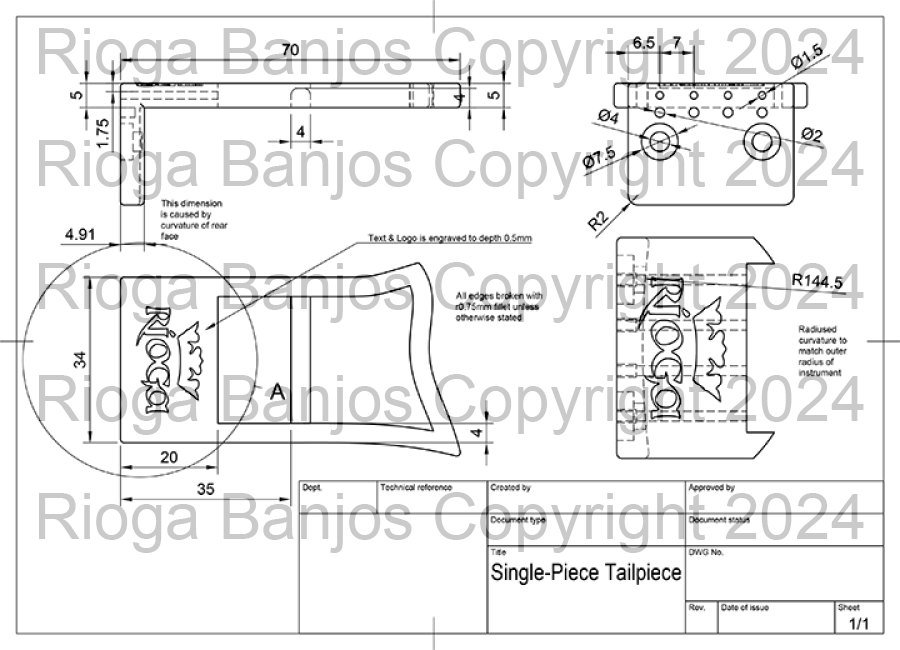
CAD (Computer-Aided Design)
We utilize CAD software to translate our technical drawings into digital formats. CAD allows for more precision, ease of modification, and the creation of 3D models. This
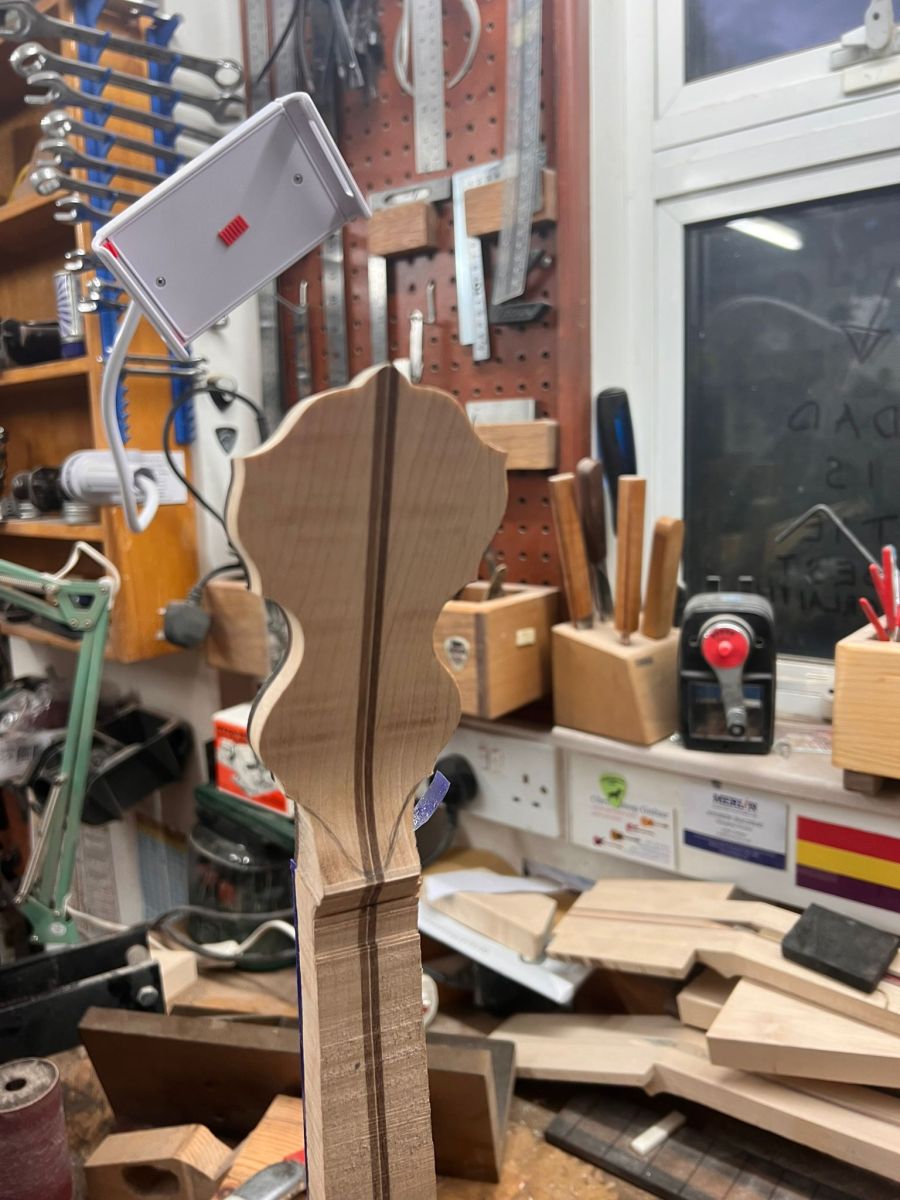
The beautiful curvature of the Rioga Maple Leaf
All of our Maple Leaf 5 piece necks are selected from straight grained maple sandwiched with Irish walnut. For our fret boards we choose ebony complimented with simple brass position markers and side dots. There is also a carbon fibre truss rod fitted for future fine adjustments if ever needed.
Precision tools used for rim cutting
We build all our rims within our workshops, this is important to us as we can maintain high standards.
Our Aims & Goals
Vintage Looks with Timeless Design
The beautiful tenor banjos of the 1920’s are irreplaceable, their designs are timeless. We aim to capture some of the remarkable features of these instruments while adding in new features of modern day banjos.
Our innovative company is redefining the art of banjo making, drawing inspiration from the golden era of the 1920s in the USA while infusing it with a touch of Irish magic. Founder partner John McClenaghan has a passion for preserving the rich legacy of the tenor banjo, now and into the future years. His dedication, precision and unparalleled craftsmanship are reminiscent of the banjo makers from the 1920’s. Each of our banjos are a labour of love, meticulously crafted to produce unparalleled resonance and tone.
Sustainable Wood Stock
Our philosophy is to hand select premium quality wood, combining it with meticulous attention to detail to ensure each banjo carries a unique character and sonic brilliance.
We source our tonewoods as locally as possible or import quality timber from reputable sustainable companies.
Quality in All Aspects
Maintaining quality is our Number One goal which is why we offer a lifetime guarantee with all our banjos.
Support of Local UK/Irish based Companies
This includes a broad range of companies i.e. engineering, metal casting, tool manufacturers and the educational sector who have been so helpful in setting up our new company.